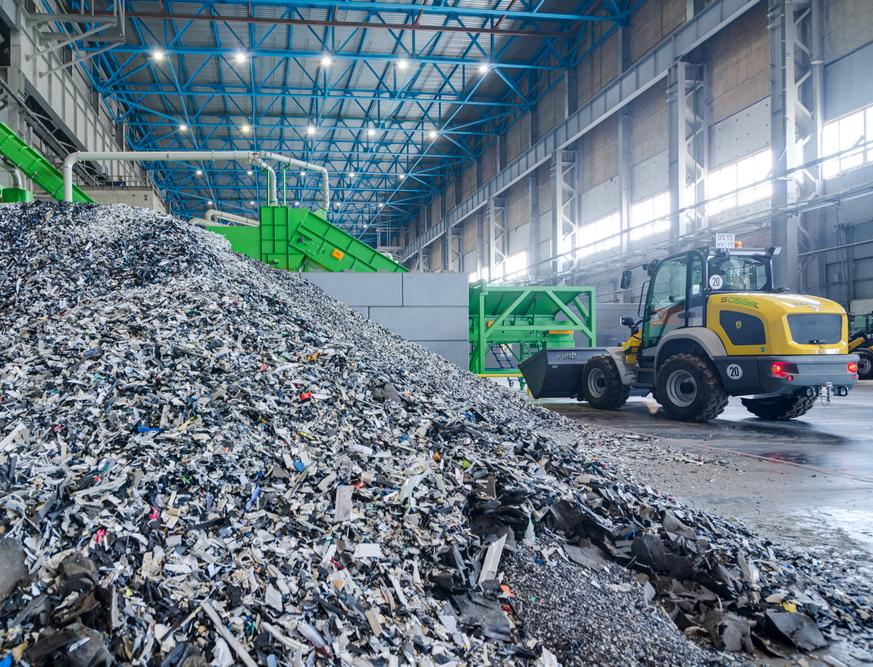
Как в России перерабатывают пластик от электронных отходов
В корпорацию «Экополис» входят три завода, каждый из которых выполняет свою локальную функцию. Первый – «Экотехпром» находится в Некрасовке, принимает электронику и разбирает ее на части: корпусной пластик и механические внутренности.
Всю пластмассу измельчают и везут на второй завод - московский «Экопласт», который занимается переработкой корпусов бывших электронных приборов. Черные металлы «Экотехпром» перерабатывает сам, а такие специфические элементы, как печатные платы, медный лом и другой цветмет отправляют на третий завод «Аурус» в Орловской области. Слаженная работа этих трех предприятий позволяет утилизировать до 95% входящего объема отходов.
В одной только Москве ежегодно накапливается не меньше 130 тысяч тонн электронного мусора. Несмотря на то, что выброшенная электроника составляет всего 5-7% от общего объема отходов в стране, попадая на полигоны, она ответственна за выделение в атмосферу, почву и грунтовые воды большого количества вредных веществ.
Любой современный прибор – это не просто «железо», а целый набор из таблицы Менделеева. В элементах могут содержаться свинец, ртуть, мышьяк, цианид, сера, хлор, не говоря уже об «обертке» из трудноразлагаемых пластиков. Поэтому так важна работа подобных предприятий и их инициативы, направленные на сбор и утилизацию электронных отходов.
Recycle рассказывает об одном из заводов корпорации – «Экопласт», занимающегося переработкой пластиков ABS, PS, PP.
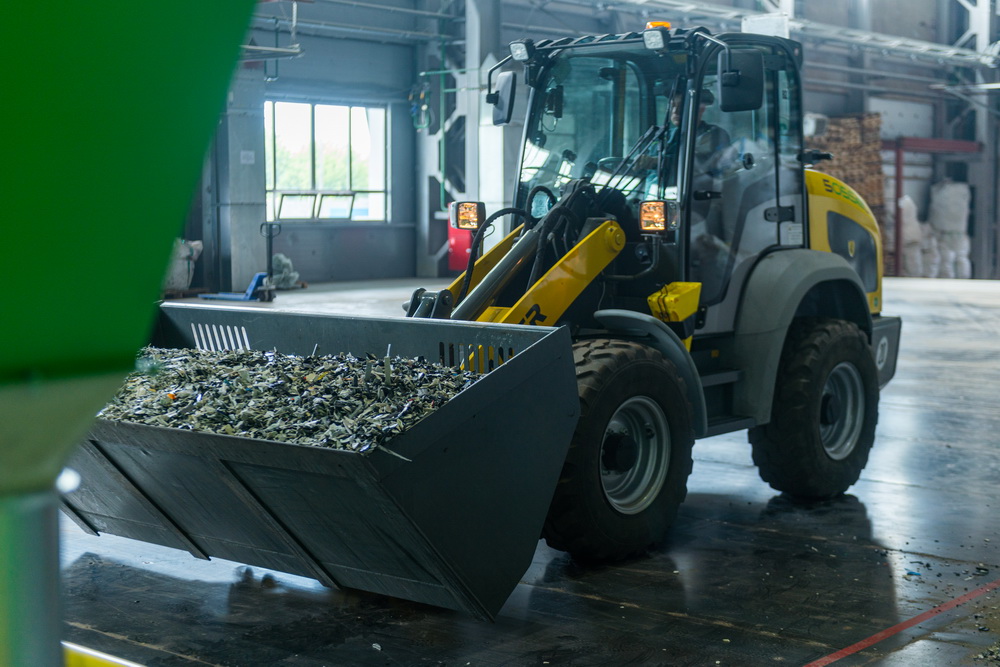
Сбор и подготовка сырья
В «Экопласт» старые корпуса приходят не только от родного «Экотехпрома», но и поставляются «с рынка» другими частными компаниями-утилизаторами электротехники. Различие видно невооруженным взглядом – сырье, приходящее с «Экотехпрома», более мелкое, однородное и не содержит большого количества посторонних примесей, в отличие от разномастного «рыночного», в котором попадаются не только элементы бывшей электротехники, но и осколки бытовых предметов (ящиков, ведер и т.д.).
«Как бы мы ни позиционировали себя в качестве рециклеров корпусных пластиков от электроники, все равно в сырье предприятий-утилизаторов могут попадаться другие предметы. Но переработке это не мешает», - рассказывает Владимир Филипенко, директор по производству «Экопласт».
Первоначально на «Экопласте» думали установить всего две линии: одну для сортировки пластиков, другую - для изготовления гранул. Функции дробления, отсева металлов и других включений должен был взять на себя «Экотехпром», где вручную разбирают каждый прибор и отправляют корпуса в мощный шредер, способный измельчить не только портативную, но и крупную технику вроде стиральных машин и холодильников до частиц размером 20-25 мм.
Поскольку спрос на переработку корпусных пластиков появился и у других компаний, которые до появления «Экопласта» вывозили такие отходы на полигоны, заводу пришлось соорудить еще одну линию для доизмельчения «рыночного» сырья и отсева примесей.
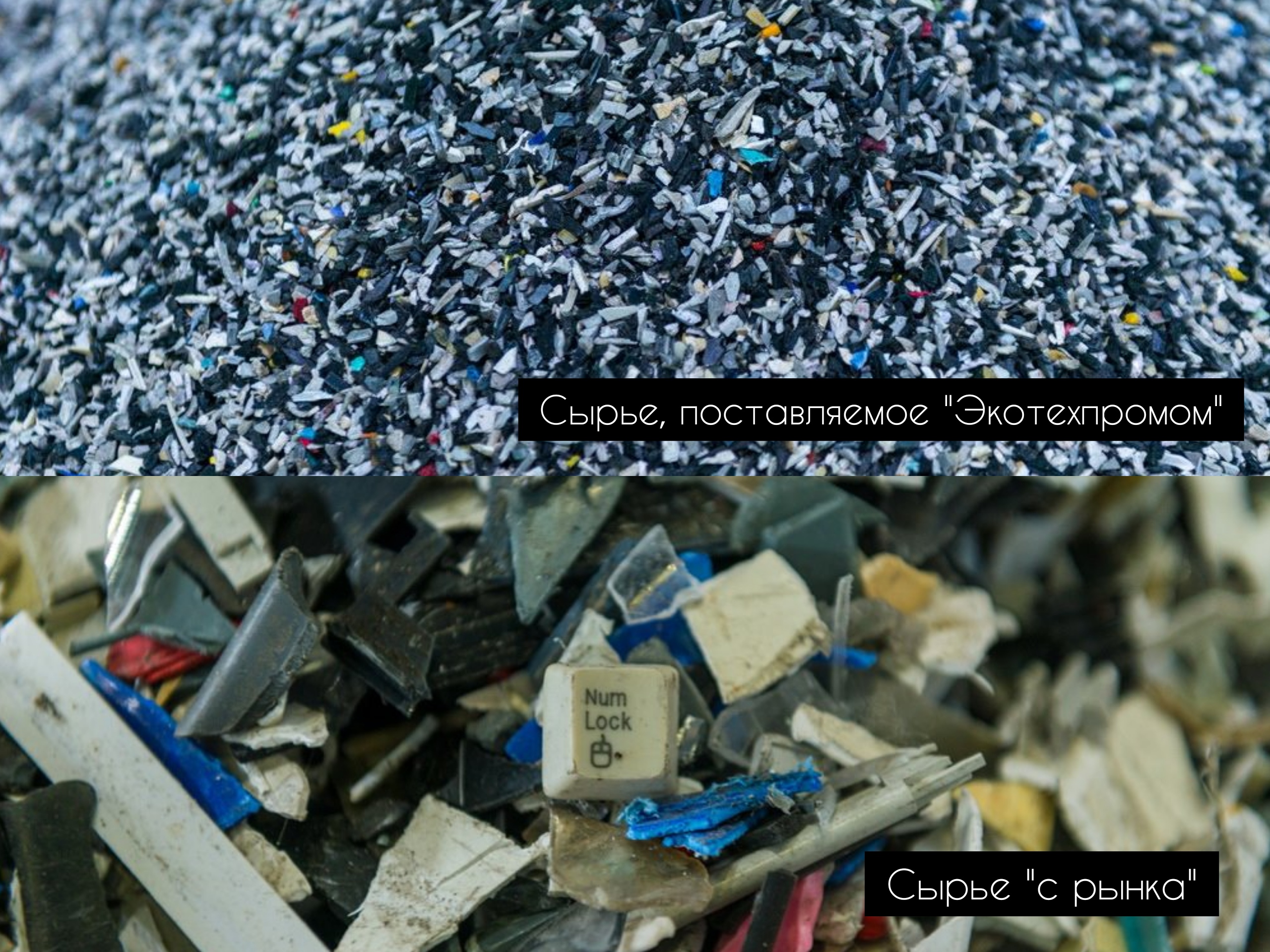
Но основной поток материала для переработки приходит все же с «Экотехпрома» - этот завод корпорации сотрудничает с крупными торговыми сетями. Люди сдают технику в магазинах на утилизацию - ее забирает «Экотехпром», разбирает и направляет по частям на два других завода - дробленый пластик в «Экопласт», а печатные платы и цветмет в «Аурус».
Сторонних поставщиков просят дробить корпуса самостоятельно, поскольку шредер, стоящий в «Экопласте», не способен справиться с объемными конструкциями, а служит лишь для доизмельчения привозного сырья.
Сдать электронику на переработку физические лица могут в магазинах-партнерах. Юридические лица могут либо сотрудничать с «Экотехпромом», отдавая им цельную электронику, либо привозить уже измельченный корпусной пластик в любом рентабельном для себя объеме на «Экопласт».
Прежде чем разгрузить самосвалы с «рыночным» пластиком, лаборатория завода берет пробы на содержание химических загрязнений, а также смотрит насколько физический состав сырья соответствует заявленному (т.к. вместо твердых фракций могут «подкинуть» мягкий полиэтилен). Если все критерии качества удовлетворены, то машины разгружают на приемной площадке, после чего ковши-погрузчики направляют материал на первую производственную линию.
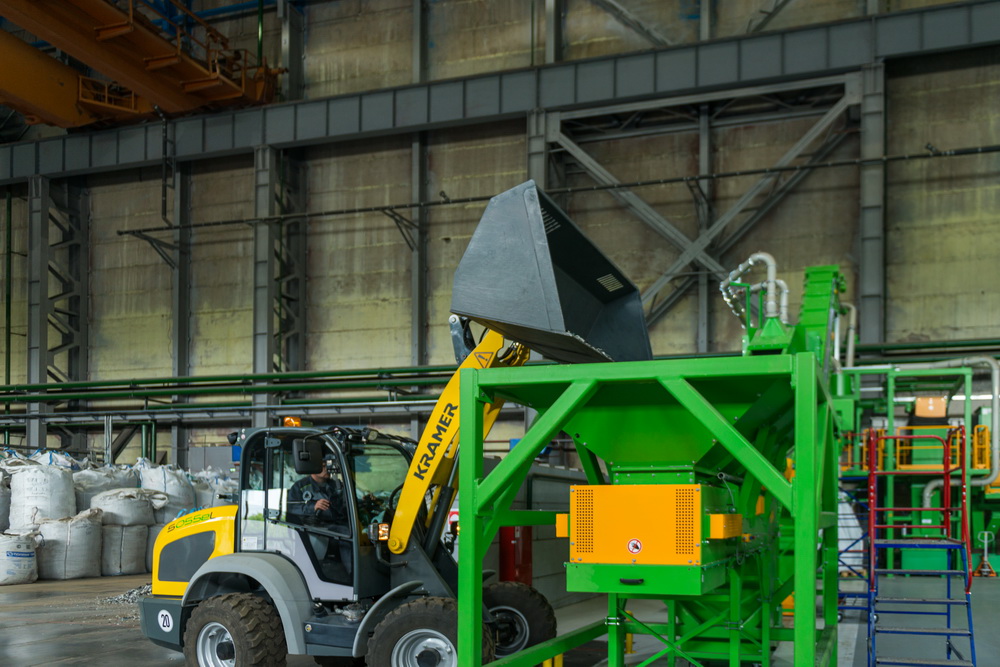
Здесь происходит не только доизмельчение крупных кусков пластика в небольшом шредере, но и извлечение посторонних фракций.
«Предприятия-утилизаторы не могут извлечь 100% металлических элементов из разбираемых ими корпусов, где-то все равно остаются гайки, шайбы и прочая мелочь, которую необходимо убрать из пластиковой массы, чтобы не испортить оборудование и избежать засорения конечных гранул», - говорит Филипенко.
После дробления материал поступает в трубопровод, внутри которого на разных участках стоят системы сепарации. На первом этапе магниты выделяют черные металлы, а система вихревых токов - цветные металлы. Далее в Z-образном сепараторе потоком воздуха определенного напора пластик выдувается в одну сторону, а тяжелые камни и стекло падают в приемник.
Во втором Z-образном сепараторе происходит отделение твердого пластика от бумаги, пленок и мягкого полиэтилена. Затем почти очищенная масса поступает на вибростол, где через сетку идет просеивание от пыли и мелкой фракции – элементы меньше 4 мм из общего потока убирают. Получившаяся смесь теперь готова идти на вторую линию, а все «ненужные» фракции сбрасываются в бигбэги (большие мешки), каждый из которых потом отправляется в свой пункт утилизации.
«Металлы мы передаем на наш третий завод “Аурус”. Стекло, перемешанное с камнями, вывозим на полигон, но таких отходов получается меньше 1%. Из всего поступающего к нам объема в новые гранулы превращается около 55-60% сырья. Все остальные пластики, переработкой которых мы не занимаемся, составляют порядка 30% (мелкие фракции, пленочный, мягкий пластик и микс heavy-пластиков). Их мы отдаем на сжигание в цементные заводы, которые используют эти фракции в качестве альтернативного топлива. Поэтому мы смело заявляем, что можем переработать до 95% входящих отходов», - добавляет Владимир.
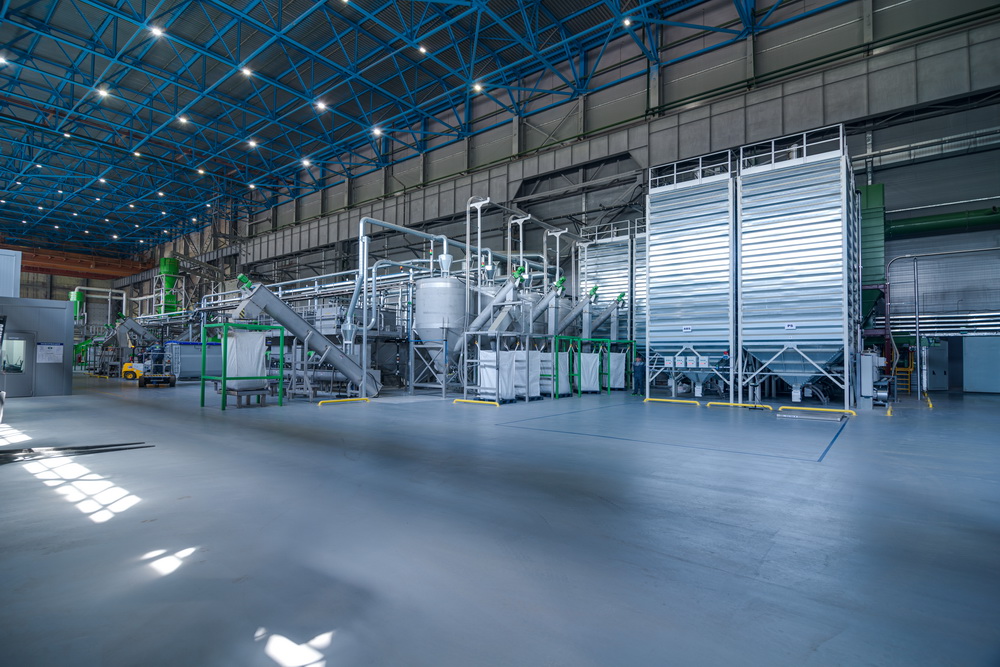
Сортировка пластиков
Сырье, приходящее с «Экотехпрома», минует первую линию и сразу же идет на вторую - оно уже достаточно измельчено и очищено от посторонних фракций, поэтому вновь пропускать его через шредер и систему сепарации не нужно. А вот «рыночный» пластик поступает на вторую производственную линию только после прохождения всех вышеописанных процедур.
Вторая линия – это сепарация пластиков в тяжелых средах. Разделение на ABS (акрилонитрил бутадиен стирол), PS (полистирол), PP (полипропилен) и heavy-пластик происходит в специальных соляных ваннах.
В первой ванной отделяются нецелевые, так называемые heavy-пластики, которые потом пойдут на сжигание. Создается раствор воды с технической солью плотностью 1.08 г/мл. Все, что тяжелее этого показателя, опускается на дно, а облегченные «рабочие» пластики всплывают вверх и по конвейеру подаются в барабанную сушилку. Далее у heavy-пластиков один путь, а у целевых - другой.
Тяжелый пластик собирают со дна первой ванны, тоже пропускают через сушилку и подают на вибростол, где происходит доизвлечение совсем мелких металлических включений - медных проволок и плат, которые потом отправятся в «Аурус».
«Мы не занимаемся рециклингом heavy-пластиков, потому что в осевшей смеси так много видов, что разделить их по типам и переработать что-то в гранулы просто невозможно. Современные пластмассы – это сплавы многих типов полимеров, в некоторые вообще добавляют мел или тальк, поэтому на первом этапе подобный материал отсеивается и уходит на сжигание в цементные заводы. Тех, кто хотел бы что-то производить из этого микса, мы пока не нашли. ABS, PP, PS - самые распространенные пластики для производства корпусов электроники, поэтому мы сфокусировались на их переработке», - объясняет Владимир.
Оставшиеся три пластика после сушки снова попадают в дробилку, которая доизмельчает целевой материал до 15 мм (необходимый размер для дальнейшего производства гранул). Затем смесь поступает во вторую ванну с обычной водой - там всплывает полипропилен. В третьей ванной соляной раствор плотностью 1.04 г/мл выталкивает наверх полистирол. Затем каждый пластик сушится уже по отдельности в барабанных сушилках и складывается в бункера-накопители, откуда потом направляется на третью линию - гранулирование.
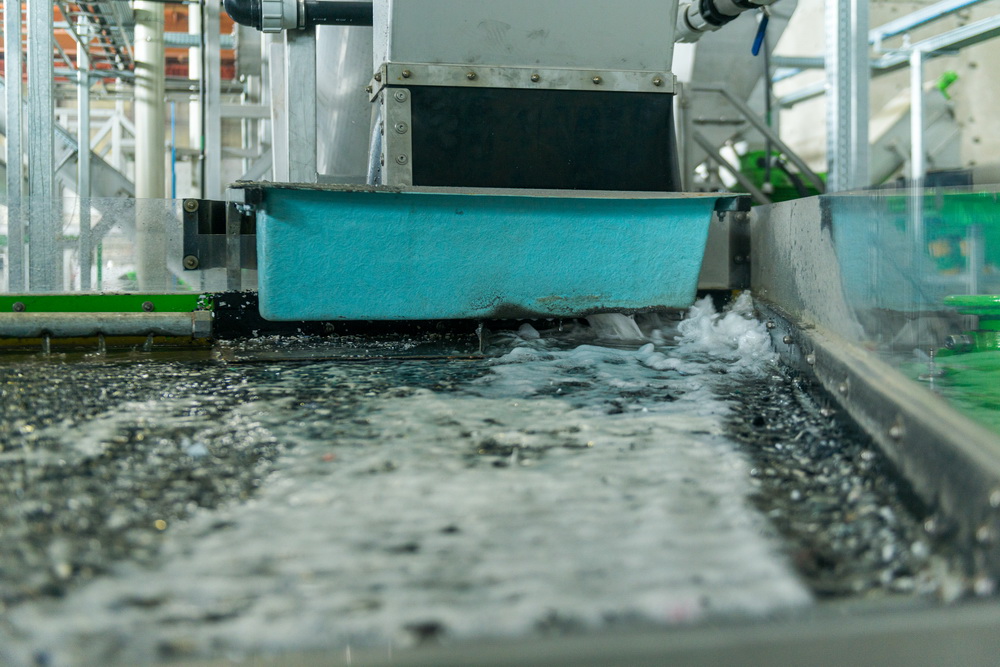
Плотность воды в ваннах ежечасно контролируют специалисты лаборатории. После того, как прошло разделение пластиков, вода не сливается в канализацию, а проходит очистку через систему фильтров. В «отработанную» воду добавляют флокулянты и коагулянты - вещества, помогающие частицам грязи оседать на ленточных фильтрах. Очищенная вода проходит сквозь отверстия в ленте и будет вновь использоваться в ваннах. Песок, грязь и прочую взвесь собирают и передают на утилизацию в цементные заводы.
В среднем около 30% от общего объема сырья составляет полистирол, 20% ABS и еще 5-10% полипропилен. Все остальное – «хвосты» на сжигание и металлолом.
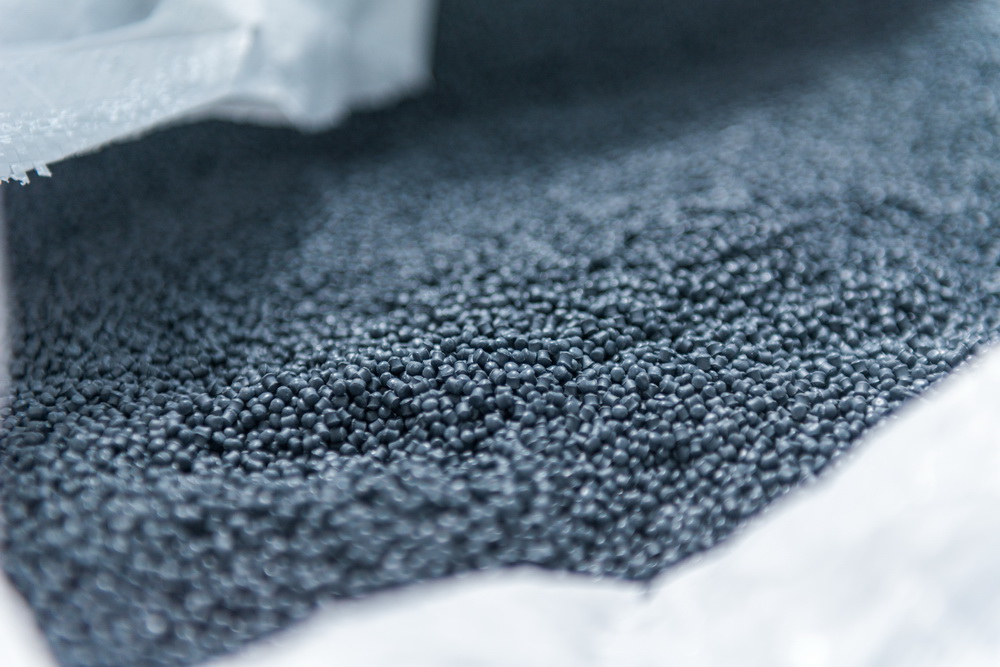
Изготовление гранул
Сердце завода «Экопласт» - экструдерная. В зависимости от производственной программы сюда из бункеров-накопителей поступает определенный тип пластика для перерождения в гранулы. Это отдельный зал, в котором находятся две сушилки - на тот случай, если влажность поступившего на переработку материала будет превышать норму, и сам экструдер.
Если с влажностью все в порядке, дробленый пластик подается на конвейер и попадает в шнековый экструдер. Принцип действия этой машины схож с мясорубкой, только при этом пластик разогревается до высоких температур, чтобы стать вязким и тягучим. Материал предварительно разогревают в бункере до 90-100°C и потом запускают в шнек (винтообразный стержень).
По мере движения по шнеку сырье размягчается, температура увеличивается до 250°C и к последнему этапу экструзии приходит в однородное состояние, в котором легко выдавливается через формующую головку. Материал, словно макароны, выходит из отверстий на 3-5 мм и срезается ножами. После чего эти кусочки подхватывает поток холодной воды и переносит на вибростол, где происходит отделение жидкости от получившихся гранул. Чтобы просушить готовый продукт окончательно, гранулы помещают в центрифугу, а после завершения процесса ссыпают в бункера-накопители и фасуют в биг-бэги для отправки покупателям.
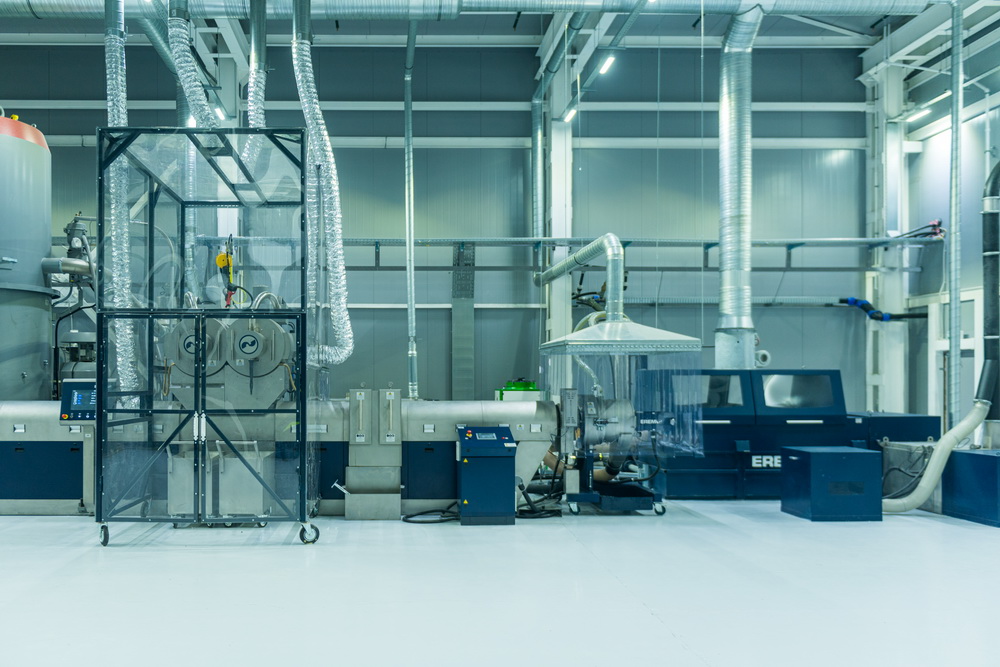
Внутри шнека стоит система лазерной фильтрации: фильтр-сетка, в котором отверстия 90 мк сделаны с помощью лазера, не пропускает посторонние элементы (вроде силикона), оставшиеся в пластике после сепарации. Также в тех местах, где возможно выделение вредных газов, стоят системы дегазации, уводящие загрязненный воздух на крышу. Там расположена еще одна ступень очищения - водяные скрубберы, где газы смешиваются с водой, и плазменные фильтры, в которых сжигаются все вредные вещества.
После изготовления каждой партии из получившихся гранул отливают образцы для проведения механических испытаний, чтобы исключить возможность брака. Готовые вторичные гранулы можно использовать для производства новых вещей либо в чистом виде, либо в качестве подмеса в первичный полимер.
«Берут как производители товаров народного потребления, так и автопром. Из этих гранул можно снова делать корпуса для электроники, вешалки, ведра, ящики, фары и другие автокомпоненты. Применение очень широкое», - говорит Владимир.
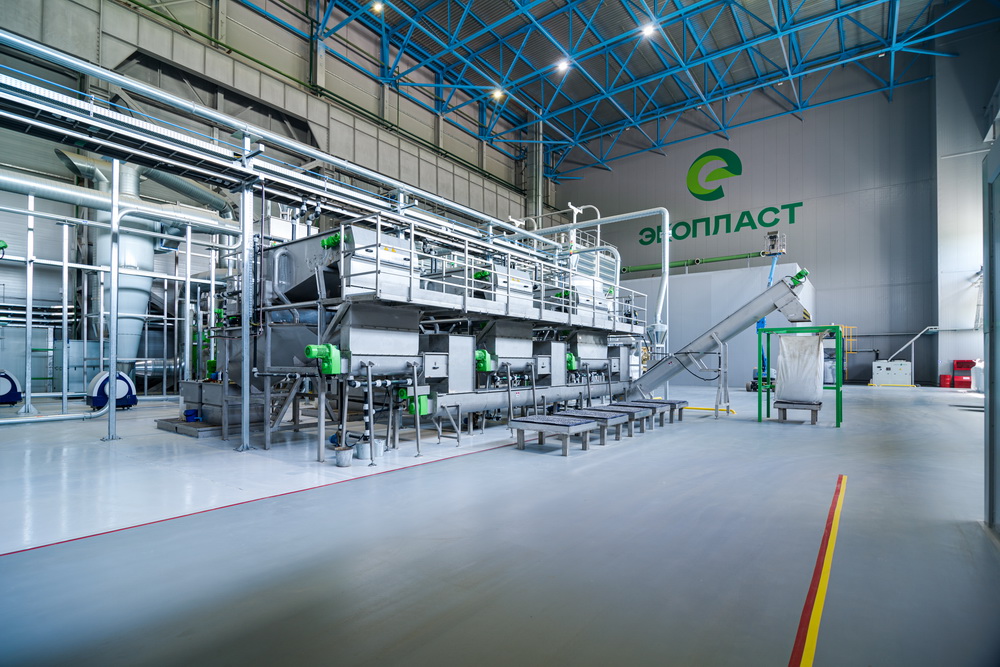