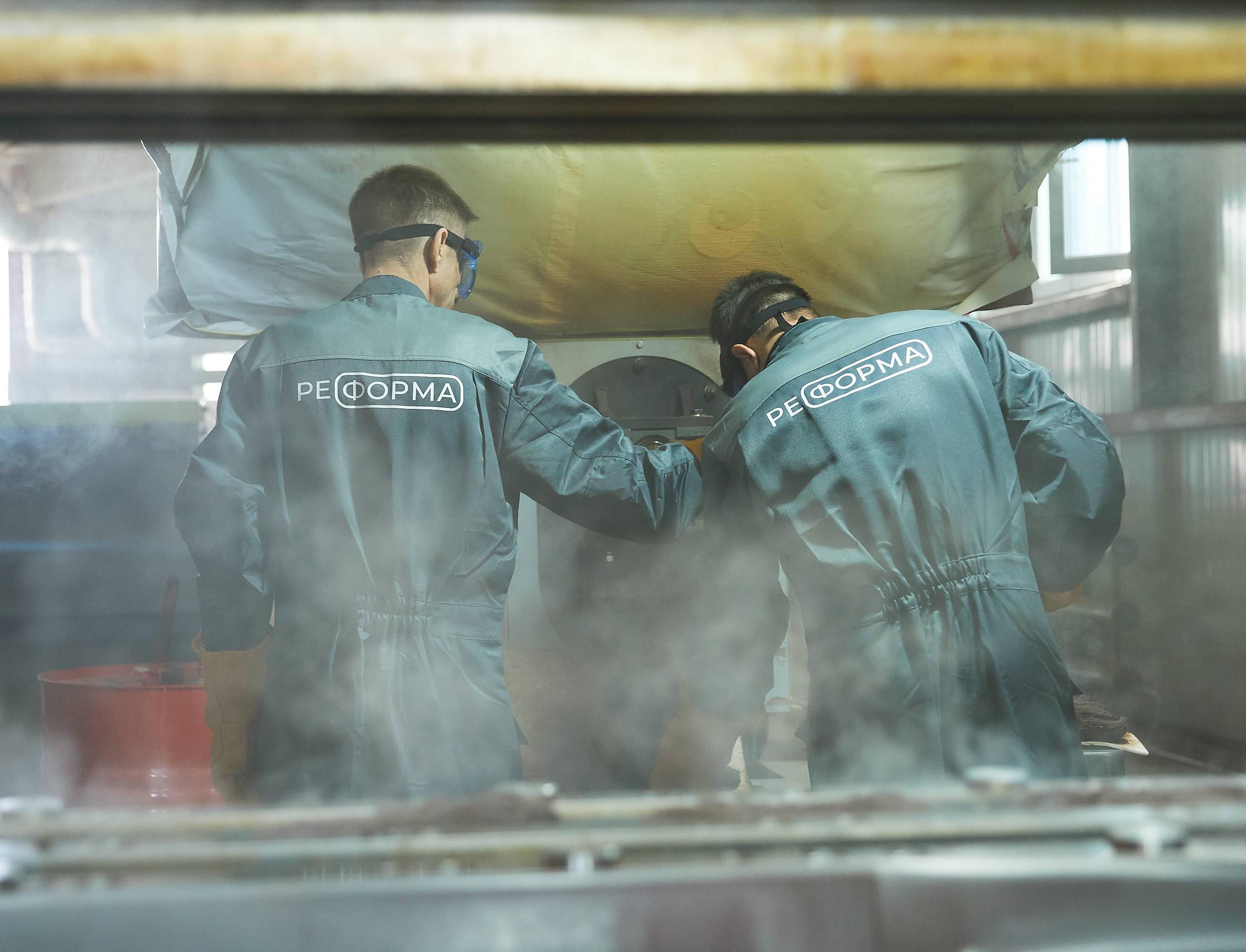
От идеи до самоокупаемости: как работает региональный стартап по переработке пластика
Ежегодно в мире образуется порядка двух миллиардов тонн твердых бытовых отходов: на Россию приходится 70 миллионов тонн, в которых доля пластика составляет около 12%. Несмотря на то, что полимерные отходы можно неоднократно перерабатывать, ниша ресайклинга пластика все еще пустует, хотя обладает потенциалом развития на десятки лет вперед.
Предприниматель Виталий Басс продумал экологический стартап РЕ-ФОРМА. Он представляет собой создание инфраструктуры для сбора пластиковых отходов, их переработки и изготовления из вторсырья элементов для благоустройства городских пространств: лавочек, урн, городских сцен.
О проекте
Для предпринимателя это стал четвертый проект, в основу которого легла идея создания малых архитектурных форм из переработанного пластика. Финансово инициативу поддержал СИБУР в рамках программы социальных инвестиций «Формула хороших дел». Так и появилась РЕ-ФОРМА.
Сегодня проект объединяет задачи по охране окружающей среды и городскому благоустройству и показывает, как вторичному пластику можно дать вторую жизнь в полезных вещах. Например, для производства одной скамьи в среднем требуется около 4-5 тысяч полиэтиленовых пакетов или 1,5 тысячи флаконов из-под бытовой химии, которые не отправятся на мусорные полигоны. Сейчас проект действует в Перми, Кстово, Свободном и Благовещенске Амурской области. В Перми, где проект приурочен к празднованию 300-летия города, уже установлено 190 лавочек и 180 мусорных баков, в Свободном и Благовещенске — около 500 малых архитектурных форм из переработанных полимеров, в Кстово установили более 40 парковых скамеек и урн, а также уличную сцену в парке.
В этих городах проходили акции по сбору вторсырья, куда можно было сдать использованный пластик. Занимались и просвещением – рассказывали жителям о важности раздельного сбора отходов и возможностей вторичного использования пластика.
Автор проекта уверен - переработка пластика решает сразу несколько задач: сокращение объема захораниваемых отходов, снижение потребления первичных ресурсов и повышение комфортности городской среды.
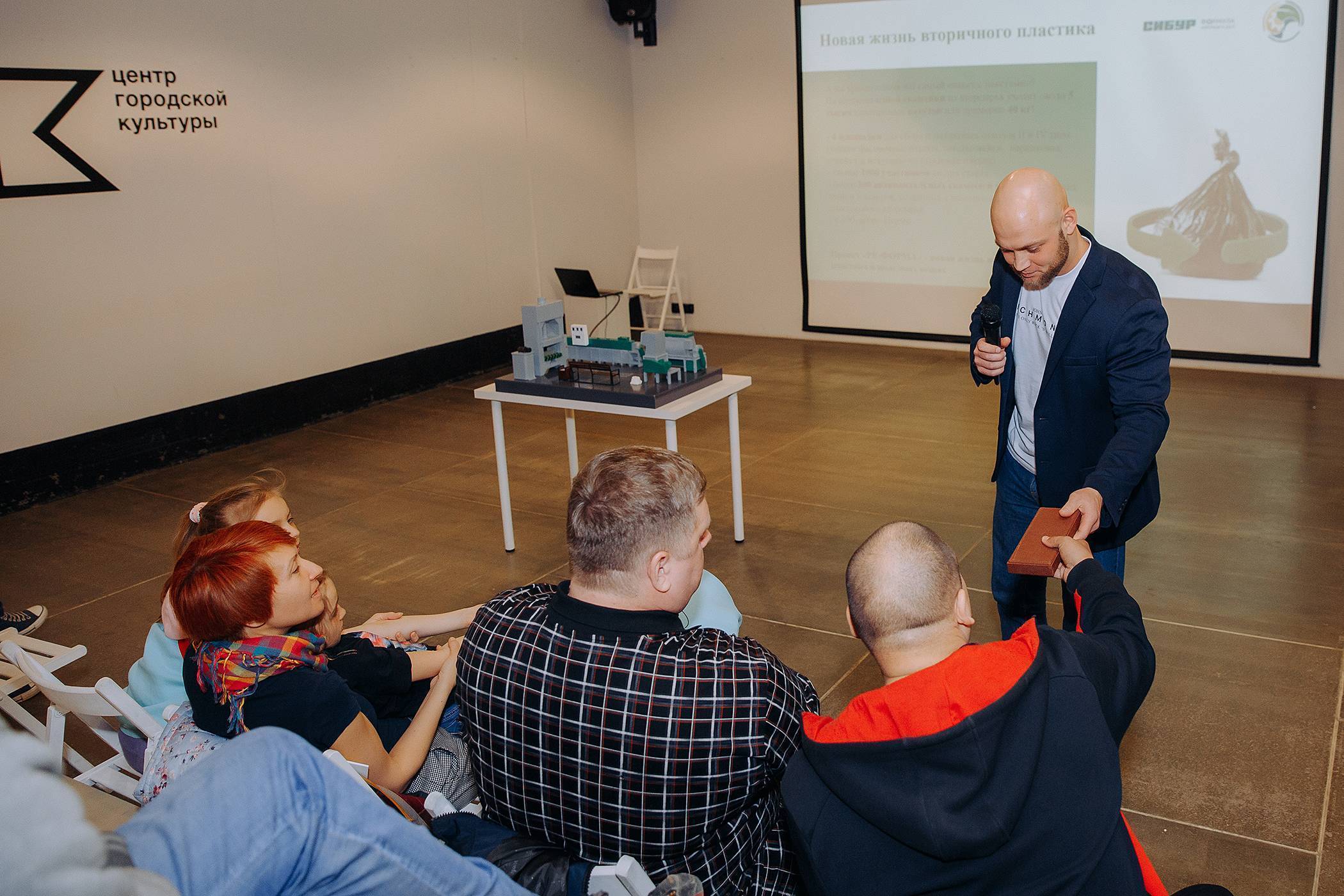
О производстве и цифрах
Производственный цикл состоит из нескольких этапов:
- пластиковые отходы дробятся с помощью промышленного шредера.
- готовится премикс – речной песок смешивается с дроблеными полимерными отходами, добавляется красящий пигмент, который придает цвет конечной продукции.
- затем специальный аппарат равномерно нагревает премикс и проводит его по восьми температурным зонам. На выходе получается однородная масса, похожая на горячий пластилин.
- масса отправляется в пресс-форму с усилием в 160 тонн и становится конечной продукцией.
За 30-40 секунд можно получить плитку, за 2-2,5 минут – ламели – продолговатые брусья, из которых собираются малые архитектурные формы.
«Подобное производство можно открыть как за 3 млн рублей, так и за 50 – все зависит от мощностей и “всеядности” оборудования – есть более капризное, которому нужен максимально очищенный ПЭТ-пластик одного цвета. Мы ориентировались на эти факторы и на обязательства перед грантодателем», - рассказал Виталий Басс.
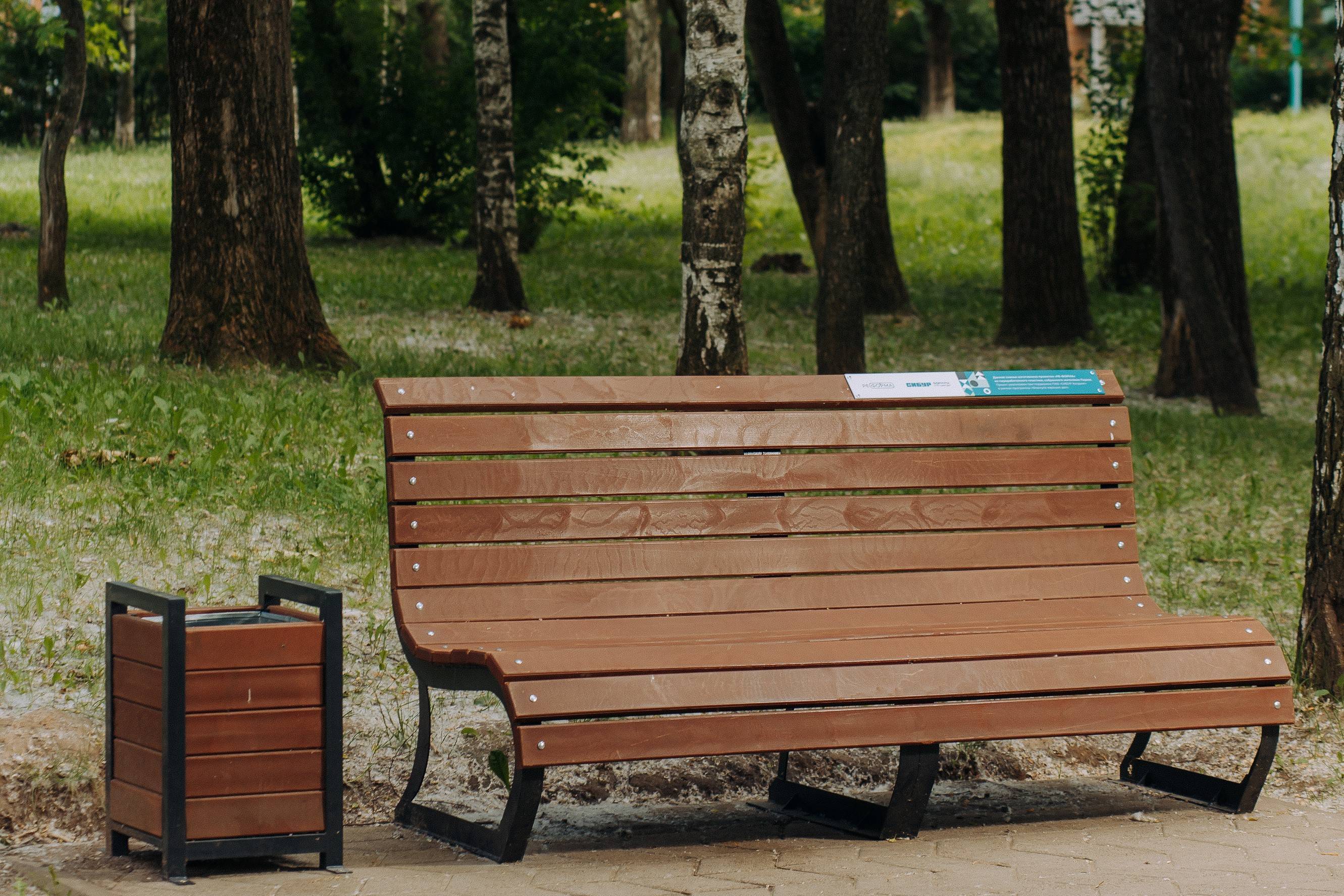
О трудностях
К пилотному кейсу в Перми предприниматель готовился полгода. С амурским проектом было чуть проще, поэтому заранее было заказано оборудование у поставщика, а для запуска использовались уже не только грант, но и собственные средства. Поэтому на Амуре получилось запустить проект всего за 2 месяца.
Но это не все. Трудности есть такие:
Сырье. Была иллюзия, что сырье будет буквально сыпаться с неба, причем бесплатно. На деле же оказалось, что даже закупить отходы не просто, за них идет борьба на рынке в формате аукциона – кто больше предложит.
Кадры. В регионах не просто найти персонал, даже когда предлагались вакансии с оверпрайсом на 30% выше рыночного. С момента старта на каждом производстве сменилось по три команды рабочего персонала. Но сейчас работает постоянная слаженная команда.
Оборудование. Поставщиков производственных комплексов, подобных этому проекту, немного. Из того, что предлагали российские производители выбиралось то, что лучше всех отвечало запросам. Однако по мере увеличения мощностей оборудование стало не справляться с задачами. Теперь удалось отдалить работу и действовать без простоев.
Логистика. Сложности возникли на Амуре, куда необходимо было отправить производственный комплекс. Зима, вес комплекса порядка 15 тонн и непростая дорога из средней полосы. Из сорока подрядчиков на работу согласились пять, а стоимость только одного рейса обошлась в 800 тыс. рублей.
О перспективах
Сейчас РЕ-ФОРМА выросла из экостартапа в полноценный бизнес. Басс отмечает, что рынок не самый простой, но очень живой и конкурентный. Для удержания позиций идет работа над разными маркетинговыми стратегиями. Например, иногда возникают вопросы, почему рыночная цена ламелей из переработанного пластика равна цене дерева.
«Мы используем этот фактор как преимущество – скамейки из дерева нужно менять раз в два-три года, красить и ремонтировать, наш материал, несмотря на равную стоимость – фактически вечная форма», — говорит предприниматель.
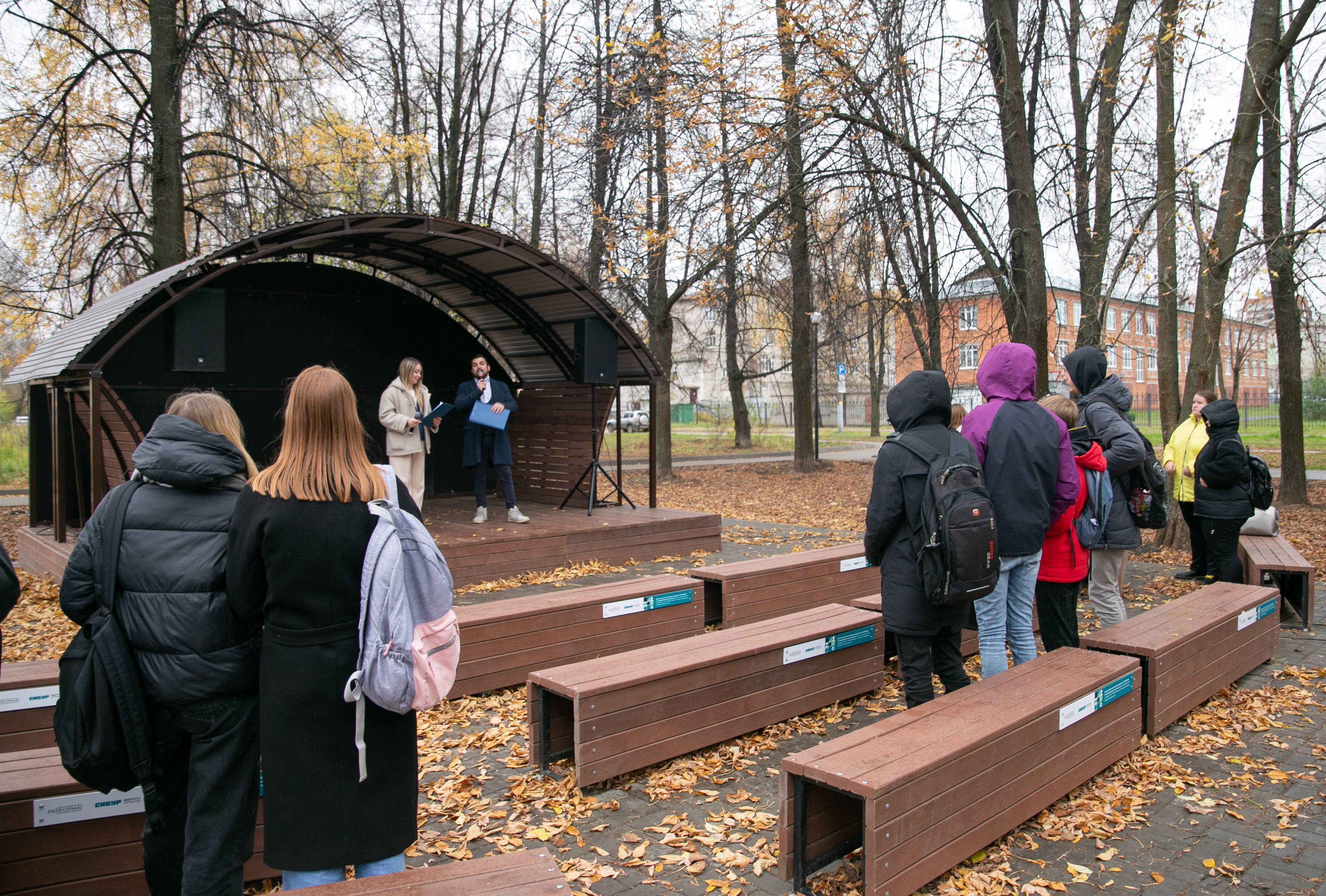
Он уверен, что рынок переработки будет расти в ближайшие десятки лет из-за всеобщего тренда на устойчивое развитие, экологической повестки государства и бизнеса и спроса на изделия из переработанного пластика.
«В наших планах масштабироваться за счет количества производств, делая их максимально рентабельными, и новых направлений — в частности, оказывая услуги по модернизации оборудования для сторонних компаний», - считает Басс.